Syntegon PMX packaging machine for ground coffee and whole coffee beans
The machine can be used for different packaging formats thanks to fast format changes and full-corner-sealing. A modular concept enables manufacturers to react fast to changing market requirements and customer needs. At the same time, the PMX fulfills modern requirements with respect to sustainability and digitalization. It processes recyclable mono-materials and reduces energy and material usage through condition monitoring.
Top features
- Up to 65 packages of 500g whole coffee beans per minute
- Recycable packaging materials
- Flexibility for different packaging formats
- Produces coffee bags with package weights between 200 and 1200 g
- Dosing, Closing stations and machine design individually configurable
- Equipped with Condition Monitoring
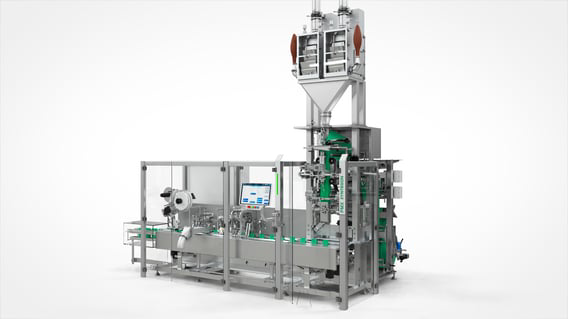
Highest flexibility through modular design
The PMX is composed of individual modules which make dosing and closing stations as well as the machine design individually configurable. Thanks to the modular structure, specific customer requirements can be realized while also achieving efficient output: the PMX packs up to 65 packages of 500 grams of whole coffee beans per minute. To reach an output of up to 100 packages per minute, the machine is also available as a double tube version. All stations are designed to process recycable packaging materials and valves made of mono-materials like polypropylene or polyethylene to meet the needs of sustainable value creation.
The PMX platform’s flexibility offers a crucial advantage for coffee manufacturers. 3D format changes on the closing unit can be achieved automatically at the push of a button. If the bag cross-section format is changed, the machine will be ready for use again after just 30 minutes. It is therefore suitable for small, medium and large packaging formats – various bag variants and closing elements can be combined. The PMX produces coffee bags with package weights between 200 and 1200 grams, both with upright and downfolded top parts. The bags are reclosable via tin tie, labels or adhesive tape. If required, manufacturers can use an innovative spout closure through which the coffee beans are emptied out at the packaging side – a convenient feature, especially for end users. The "neutrafill" process, in which the coffee is gas-flushed before and during the packaging process, ensures aroma protection.

Full-corner-sealing for attractive product presentation
To make the best use of the print area and ensure that the label is easy to read, the full-corner seal does not have longitudinal seams on the back of the packaging. “This type of sealing not only looks attractive on the shelf, but also pays off in terms of sustainability. By positioning the full-corner-sealing module in the front area of the forming tube, the packaging materials can be retracted within just a few cycles – which reduces the loss of material significantly”, says Dr. Hans Albrecht, project manager at Syntegon.
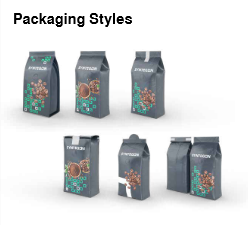
Lowering the height of the machine reduces the cycle time, which enables higher packaging speeds. This also results in a lower drop height for the coffee beans, which reduces the breakage rate and rejects significantly and leads to better ergonomics for format changes. The full-corner-sealing can be retrofitted to existing PMX machines at any time. Manufacturers can thus plan for the long term with the machine even in case of design or format changes.
Latest sensor technology monitors resource consumption
To keep energy consumption as low as possible, the PMX is equipped with condition monitoring. In addition, the consumption of inert gas and packaging material can be digitally monitored and controlled. Machine data is collected in real time and clearly displayed on dashboards.
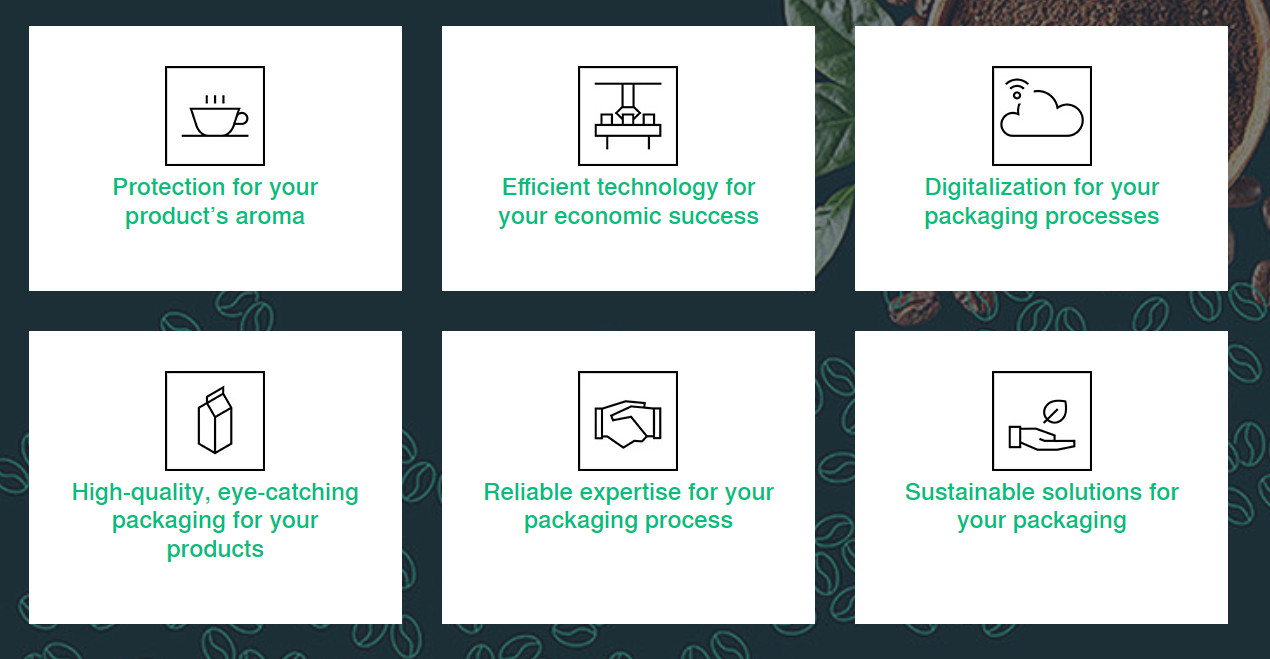